Polyphenyl Ethers; OS124; OS138
Polyphenyl Ethers were originally developed for military jet engines due to their thermal and oxidative stability and resistance to radiation environment. The first commercial application of PPE was in 1964.
Using 1% solution of OS124, the wear failure of gold plated contact ( figure 1) virtually drop to zero. Since then, connector manufacturers have used them in various plated materials and applications.
Many studies have been conducted, and these are some of the advantages in using PPE lubricants.
1. Outstanding thermal and oxidation stability 2. Good resistance to chemicals and radiation.
3. Good lubricity 4. Corrosion inhibition
5. Good wear resistance 6. High surface tension ( does not migrate)
7. Low vapour pressure 8. Disperse dust and prevents contact problem 9. Resistance to **fretting corrosion
10. Reduce gold plating thickness for the same life-span of connectors.
11. Extend times to failure of a connector by 2~100 times.
12. Able to restore contact failure due to fretting corrosion. ( figure 2)
These lubricants (usually diluted) can be applied at the end of plating line, before or after soldering or on the electronic assembly even the breakdown or failure has occurred. This will serve to retard further corrosion and provide increased life for the connector and electronic or electrical component. The application is simply by spray ( normal spray bottle or aerosol can) or dipping.
**Fretting corrosion: This corrosion is the result of a small scale movement ( micromotion) of a few tens to a few hundreds of micron in mated connectors. Its movement can be due to minute temperature changes, vibrations, assembly, shock impact, transportation etc etc.
This causes the degradation of noble metal like gold, palladium and oxidation in Tin/lead alloy metal, and impede the movement of electrical current which leads to loss of transmission of data, loss of connection, heat build up, higher energy consumption , etc etc, problem prevalent in both new and old mobile phones, computers, electronic devices.
From cell phones to computers to specialized medical equipment, more system failures are caused by electronic connectors than by individual components, even though components are usually thought of as being more fragile. PPEs give electronic connectors a long-term reliability that will outlast the life of the system.
An experiment using a 50g force was place on a non lubricated pin. After 3,600 cycles it was badly abraded and failed. When identical pins were coated with a PPE layer using the same parameters, no damages were found on either pin after 500,000 cycles ( arbitrarily ended).
Uses:
Extreme high temperature fluid eg jet engine turbine lubricants
Chain lubricant
Connector lubricant
Optical gel and fluid
Radiation resistance fluid and greases High Vacuum pump fluid
Prevention of fretting corrosion can be by done by:
a) high contact force b) using PPE as a contact lubricant to prevent oxidation.
However, exerting high contact force will wears the surface of the contact faster, and over a period of repeated mating, leads to a complete failure of transmission.
Figure 1
The effects of micro-motion on the surface of a connector pin: abrasion at center, surrounded by a debris pile consisting of oxidized and unoxidized particles
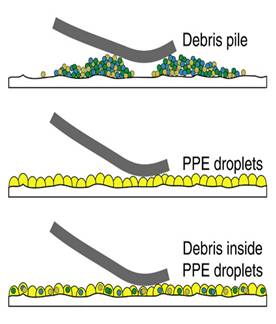
Figure 2
Micro-motion leads to corrosion, which produces debris piles (top) that eventually push the pin away from its contact. Application of a PPE (center) creates a field of microscopic droplets that prevent abrasion and corrosion, yet permit electrical conduction. If an already corroded pin in treated with a PPE (bottom), the droplets capture the debris particles and conductivity resumes.
|